Hello again,
Following on from my intro post here are some details of the start of my build from January onwards this year.
Firstly I needed a flat surface to work on. I put together a 12 foot by 2 foot table with MDF surface. Here it is looking new and shiny before I ruined it will loads of glue and filler -
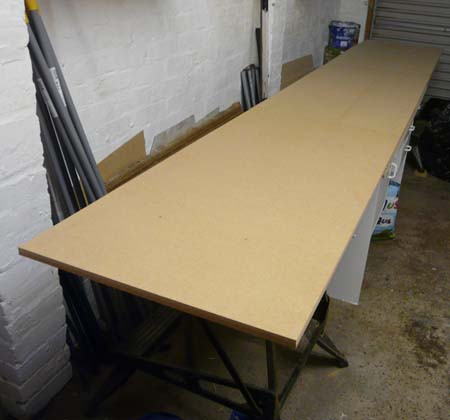
Secondly I needed to get plans printed off. The two main plans were printed off in 360th scale, which means I simply need to multiply any distance on those plans by five to get 72nd scale. In addition printing off all drawings in full 72nd scale would prove to be really helpful. This was more of a problem as, you've guessed it, most printers on the high street don't print off 15 foot X 7 foot plans. Instead I got 33 separate plans printed off in A0 paper size (841 x 1189 mm) online from
www.planprintinguk.com. I then sellotaped the A0 size plans together to provide all the 1/72nd plans I require. Here is one of the plans on the driveway -
The Nimitz model on top of the plan is in 350th scale (roughly one-fifth of 72nd).
I needed plenty of screengrabs from the movie so I took 370 shots showing all the planes and the ship itself. This was a good excuse to watch the movie again, not that a reason is needed. Have you watched it yet?
When building a wooden model you do, at some stage, have to buy wood. The hull frames are in 6mm thick marine ply whereas the skin will be in 4mm marine ply. Both are purchased in 8 foot by 4 foot sheets. So far I have bought 3 sheets of 6mm and 6 sheets of 4mm marine ply.
I also bought wood for the stringers (stringers go between the frames, with the ply glued to the stringers). The thick ones for the midsection of the hull are 14mm by 28mm so quite strong; I bought 134 feet worth of that and have already run out and have had to buy another 56 feet worth. For the bow and stern I am thinking of using thinner stringers 36mm wide by 6mm deep; so far I have got 65 feet in that size.
Other items on the shopping list were 9mm MDF for the table, 2 big tins of 2-part car body filler, 2 tubs of 2-part wood filler, 4 tubes of wood filler, 7 tubes of bathroom sealant, an electric sander with sandpaper, bandsaw, 100 disposable gloves, 72 20g bottles of Turbo CA glue, 4 large 400ml cans of accelerator, 11 large sheets of plasticard, Colourcoats enamels for the 350th kit, sandpaper, 20mm and 22mm holesaws, 15 steel broom poles, one long steel rule, 6 clamps and 50 sheets of carbon paper. Thankfully I already had a pencil.
The first build task was to draw the hull frames lines onto the 6mm ply. There are 16 frame lines in total, numbering 0 to 15. To draw the hull lines I added carbon paper under the plan and drew the lines with pencil. Here are the sheets on top of 6mm marine ply -
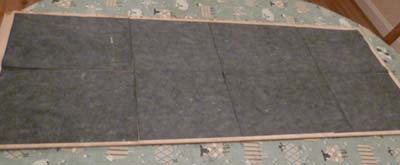
Now here is the plan directly on top -
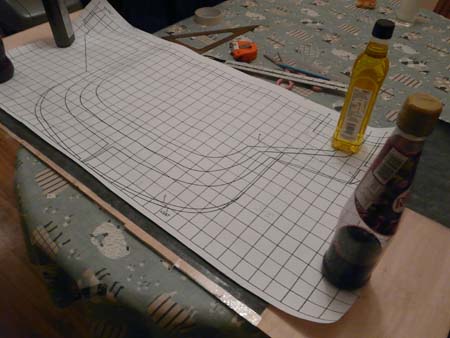
Then it was a case of carefully cutting out the frame lines using my new bandsaw. Here can be seen my test run on a scrap piece of wood -
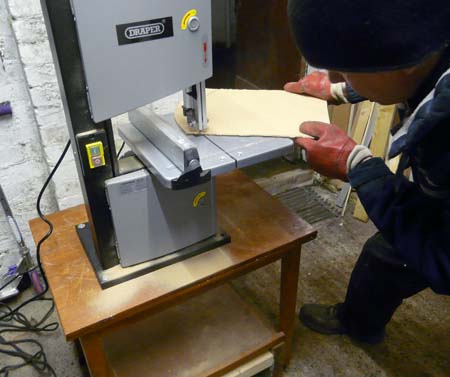
So far I have not needed any emergency procedures due to bandsaw or jigsaw mishaps. All eight fingers and both thumbs remain attached to my hands. However this may change. If you hear reports of an idiot modeller trying to glue a finger back on with Turbo CA glue that will be me.
Hull frame photos to come tomorrow.
Cheers,
Dougie